Explaining chemical recycling processes
- Vasilakis Nikos
- 25 Ιαν 2022
- διαβάστηκε 6 λεπτά
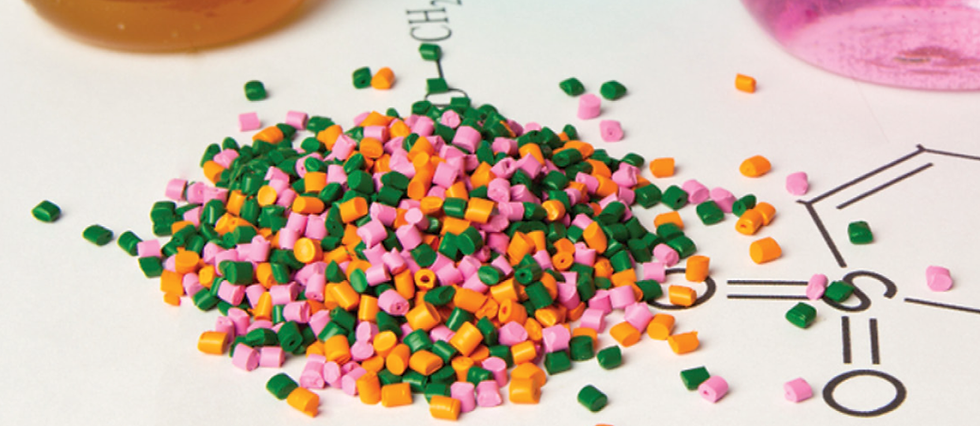
Chemical recycling is an umbrella term that includes a variety of technologies, each with their own process characteristics, input requirements and outputs.
Few in the plastics industry will not have heard of chemical recycling but that simple term covers a
huge range of quite different technologies. Today’s chemical recycling technologies can be classified into three broad concepts: dissolution, depolymeri-
sation, and thermal cracking.
These three approaches differ, at a conceptual level at least, in the type of materials they can handle, the amount of “chemistry” involved, and the product that results.
Dissolution technologies use carefully selected solvents to dissolve the polymer from the mixed
waste, allowing insoluble contaminants such as fillers and pigments to be filtered out. The dis-
solved polymer can then be precipitated and recovered from the solvent, which is reused. This is
a physical process — the chemical composition and structure of the polymer is unchanged.
As a result, many of its proponents consider it to be closer to mechanical than chemical recycling and promote it accordingly, using terms such as solvent-based purification or physical or material recycling. The key to success in dissolution is the selection
of a solvent that recovers only the target polymer. This means it is best suited for use with relatively
homogenous waste streams. A number of pilot projects are already well advanced — Purecycle
Technologies in the US, for instance, is targeting polypropylene with a technology licensed from
P&G while Canada’s Polystyvert is focusing its efforts on polystyrene.
The need for a relatively homogenous waste stream does not necessarily mean that dissolution
technologies are suitable only for mono-material plastic waste. Germany’s APK, for example, is
developing its technology to recover LDPE and PA from multi-layer films.
In theory, at least, dissolution exposes the polymer to less thermal and physical stress during
the recovery process than conventional mechanical recycling. However, the recovered polymer is likely to require compounding or pelletising to make it suitable for further use, which may mitigate that benefit to some extent. In addition, the cost of the numerous processing steps — pre-treatment,
dissolution, filtration, precipitation, solvent removal and reformulation — is likely to make dissolution
most attractive for processing of mono-material waste streams with a relatively high level of
contaminants that would be difficult to remove mechanically otherwise.
Depolymerisation is certainly a chemical recycling process, typically using heat (and often a
catalyst) to convert a polymer back to its building block monomers — for this reason it is sometimes
referred to as monomer recovery. It is most suitable for use with step-growth polymers such as PET,
which are polymerised by polycondensation.
A number of companies are developing various processes to depolymerise PET, with pilot projects
underway at Carbios in France, CuRe Technology and Ioniqa in the Netherlands, Rittec in Germany, and BP Infinia, Eastman and Loop Industries in
North America.
Depolymerisation of polycondensation polymers typically involves reintroducing the molecular
component that was eliminated during the original polymerisation process. Several solvolytic processes are being investigated to do this, including hydrolysis, glycolysis, methanolysis and transesterification. These are all multi-step processes that include pre-treatment of the waste, followed by depolymerisation, monomer recovery, repolymerisation, and finally extrusion and pelletising.
Solvolytic depolymerisation techniques are not suitable for use with polymers produced by
chain-growth or polyaddition reactions, such as PE, PP and PS.
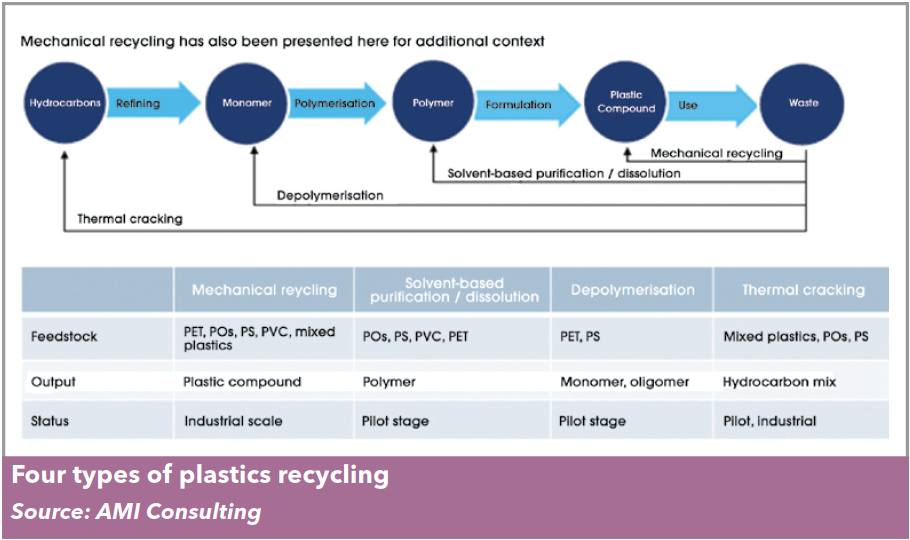
However, some companies — including Pyrowave in Canada and Agilyx in the US — are
working with alternative thermal depolymerisation technologies that are capable of converting PS
polymer back to styrene monomer.
By converting polymers back to the original monomers, depolymerisation can lead to new polymers of virgin quality. However, it uses highly specific chemical processes so the incoming waste
stream has to be consistent in terms of polymer composition, meaning considerable cost may be
incurred in pre-sorting. Energy requirements can also be quite high.
Thermal cracking converts waste plastic – and many of the contaminants the waste may carry – back to basic feedstock components such as hydrocarbons
and syngas (a gaseous mixture of CO, CO2, H2 and CH4). Two processes are used to thermally crack – or feedstock recycle – polymers: pyrolysis cracks the
polymer chains at high temperature in the absence of oxygen; gasification heats the polymer with a
controlled but limited amount of oxygen. Both yield a different mix of end products with targeted applications ranging from fuels to chemical feedstocks.
Conventional pyrolysis thermal cracking is a relatively simple technology. Waste goes through a
pre-sorting and shredding process and is then pyrolysed at high temperature — typically 400-600°
— to create vapour and gas, which is then purified to create a range of hydrocarbons. These hydrocarbons can include gas, wax, oils and char. Yields of each can be controlled to some extent by adjusting temperature, pressure, and residence times, as well as through the use of particular catalysts and thermal profiles.
As pyrolysis occurs in the absence of oxygen, the process is only really suitable for polymers with
a limited oxygen content, such as PE, PP and PS. Polymers containing high levels of oxygen or
halogens — particularly PVC and compounds containing brominated flame retardants — must be
sorted and removed from the waste input stream.
Oxygen and halogen concerns aside, pyrolysis can handle waste streams with a mixed polymer
composition that would be highly challenging for either mechanical or dissolution and depolymerisation chemical recycling methods. That said, it is an
energy intensive process and the quality and mix of the output materials is still dependent to some
extent on the input materials. In addition, much of the gas and oil output from pyrolysis plant is likely to be burnt as fuel, either to provide energy for the process itself or because of the need for additional purification steps to upgrade it to be used as a cracker or chemical plant feedstock.
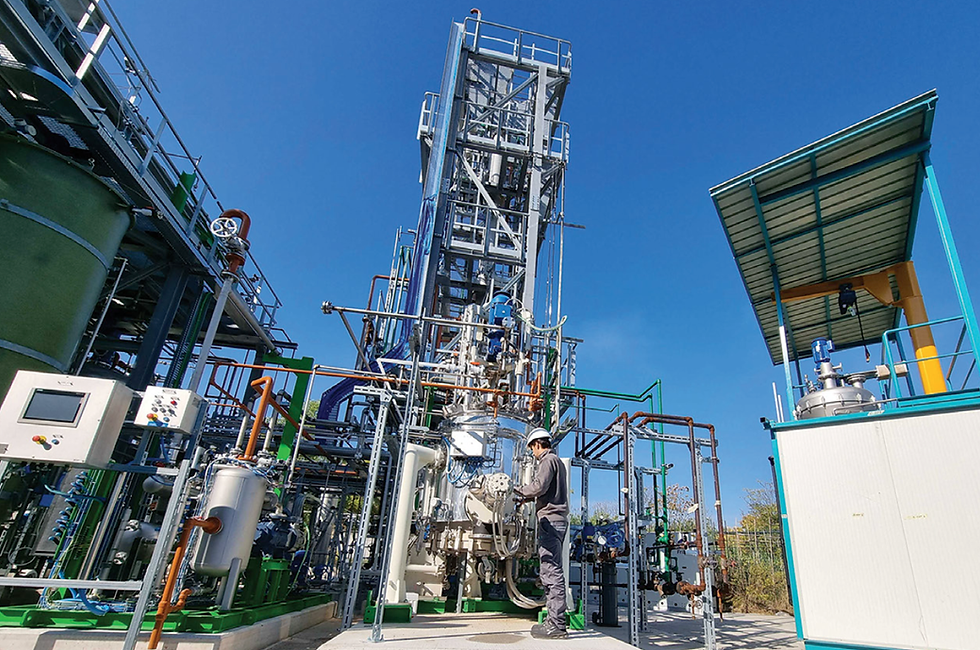
Major players in the development of pyrolysis-based technologies include Luxembourg-head-
quartered Clariter, Enval, Recycling Technologies, Renew ELP and Plastic Energy in the UK, Fuenix
Ecogy in the Netherlands, OMV in Austria, Quanta-fuel in Norway, Brightmark, Encina, Nexus Fuels and Alterra Energy in the US, GreenMantra Technolgies in Canada, and Licella in Australia.
Gasification thermal cracking differs from pyrolysis in that the process takes place in the presence of a controlled but limited amount of oxygen. It can handle almost any organic material — including
plastic waste and biomass — and can take on polymers containing oxygen and halogens. The end result is syngas that, depending on its composition and purity, can be used as a production feedstock.
The gasification process involves fewer steps than pyrolysis: pre-treatment of the waste (including
water removal); gasification; and cleaning of the gas to remove tars and other contaminants. That final purification step is required to remove impurities such as ammonia, H2S, alkali metals, NOx and tars.
Gasification is not a new technology. Texaco developed and licensed its TCP (Texaco Gasifica-
tion Process) technology back in the 1980s to handle hazardous waste organics. It is a non-cata-
lytic, partial oxidation process capable of converting organics to syngas and chars. However, the TCP process does not produce feedstocks suitable for reintroduction into plastic-to-plastic or other
value-added chemical synthesis chains.
A number of companies are investigating gasification processes to crack plastic waste to
heavy oil and non-condensable gases and condensable gases. The non-condensable gases are used as process fuel while condensable gases and heavy oils can be gasified with oxygen and steam. These processes typically involve use of high temperature gasification at more than 900°C, which is energy intensive, followed by additional purification steps.
Gasification thermal cracking technologies are under development by a number of companies,
including Enerkem in the Netherlands, Eastman in the US, and Showa Denko and Sekisui/Sumitomo in Japan.
Chemical recycling is still a very young technology. However, it seems clear from the work carried
out to date that hopes that it will solve the challenge of handling mixed waste streams may be
misplaced. The reality is that most of the technologies currently under development will need some
level of homogeneity in waste feedstock. That means that, initially at least, chemical recycling is
likely to draw on the waste sources and supply
infrastructure developed for mechanical recycling.Drawing on the same collection and sorting
infrastructure does not necessarily mean that chemical recycled material will compete directly
with mechanical recycled material. Compared to mechanical recycling, all chemical recycling
processes are more complex and are likely to be more costly. So, where high quality waste streams
are available, mechanical recycled polymer is likely to win out simply on economics.
Chemical recycling, on the other hand, begins to look a lot more attractive where waste streams are less homogenous than is preferred for mechanical
recycling, or where volumes of recycled material exceed the capacity for reuse in new applications
(either for reasons of regulation or for deterioration in material properties).
There may be some competition for feedstocks, but even that is likely to be limited. I
Looking at feedstocks for the thermal cracking processes — either pyrolysis or gasification — that
are expected to account for the majority of chemical recycling in volume terms, the fact that mechanical recycling can only offer a “downcycling” solution for mixed plastics waste
makes it a prime stream for the chemical route.
CW magazine
More
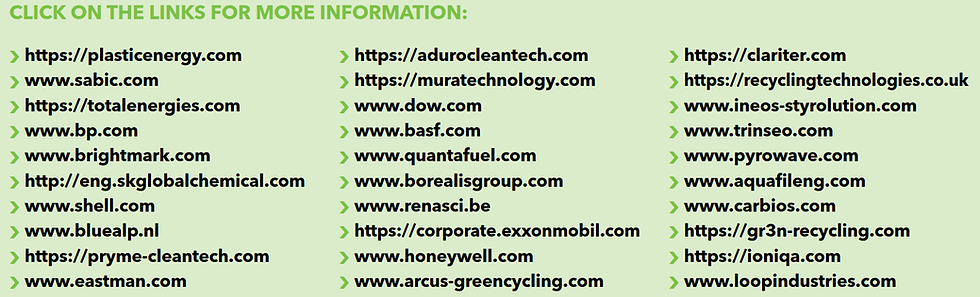
Comments